Plant Guide
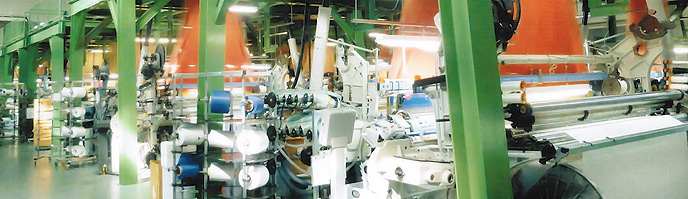
Process
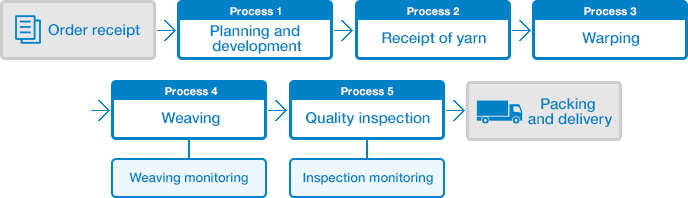
Plant Guide
1. Planning and developmentOffice
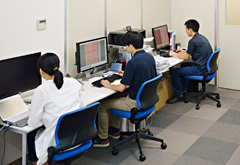
The fabric is designed, planned and developed based on the customer’s request.
Information on the structure, yarn type, weft exchange instructions, yarn density, warp alignment, etc. is input. The fabric is printed and simulated.
The patterns are also simulated.
The image and texture can be checked and examined closely before starting the actual weaving process.
2. Receipt of yarnYarn warehouse
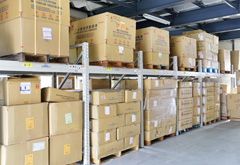
The received yarn is stocked in the “Yarn warehouse”.
- The warp yarn is delivered to the preparation plant and warped.
- The weft yarn is delivered to the 1st and 2nd weaving plants.
3. WarpingPreparation plant
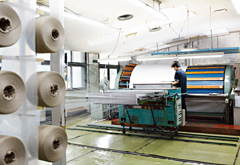
- The warp yarn delivered from the “Yarn warehouse” to the “Preparation plant” is beamed at the preparation plant.
- The warp yarn is beamed at a stable tension without damaging it. The sensor checks for abnormal yarn.
4. Weaving1st and 2nd weaving plants
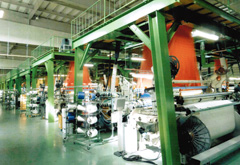
- The advanced electronic jacquard high-speed rapier weaving machine enables fast, high-quality weaving.
- The sensor detects abnormal warp yarn.
- Multiple functions including weft density change and speed control are provided.
- High-speed weaving at low tension to prevent yarn damage is possible.
- The air splicer prevents warp breakage.
- The weaving conditions are monitored by the weaving machine monitoring system.
5. InspectionInspection room
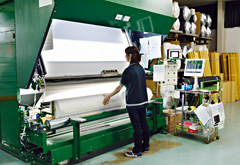
- The fabric information is simply input to the computer using bar codes and a touch panel.
- The fabric is inspected with variable intensity. High operability is secured at the optimum brightness to detect flaws.
- Problems can be promptly solved by monitoring in the inspection room.
- The inspected fabric is rolled and shipped.